In the Spring of 2016 at the University of Alabama, I taught a brand new course titled Aircraft Systems under the course number AEM 617. Topics under consideration included:
- Nomenclature (Sample Notes: Lesson01-Introduction)
- Standard and Non-standard Atmospheres (e.g. Moist Air Density)
- Airspeed (Flight Data Computer Calculations)
- Vacuum Systems
- v-n Diagrams including gust loading
- Basic 4 bar mechanisms (e.g. slat & flap extensions) and Freudenstein Equations
- FAR 23 (14CFR23)
- FAR 25(14CFR25)
- Cockpit Layouts
- Flight Control Systems including equations of motion, gear ratio
- Aircraft Hardware (e.g. AN bolts, rivets, etc.)
- Hinge Moments (Guest Lecture)
- Nonlinear Systems Phase Plane Analysis
- Hydraulic Systems including Actuators, PCU (Power Control Units),
- Fuel Systems including Inerting Systems and Refueling
- Pressurization Systems (Guest Lecture)
- Test Flight Systems and Instrumentation (Guest Lecture)
- Communication and Navigation
- Environmental Control Systems (ECS)
- Emergency Systems
- Survivability
- Inertial Navigation Systems including World Reference Frames, and Strapdown Equations
- OBOGS (Onboard Oxygen Generating System) (Guest Lecture)
- Kalman Filters
- Electrical Systems and Wiring (Guest Lecture)
- Morphing Wings (Guest Lecture)
- Software Development and Modular Avionics Bus
- A brief description of IEEE 754 floating point numbers
- Spacecraft Attitude (Guest Lecture)
- Propulsion (Guest Lecture)
- Multi-Engine Vmc
The notes contain numerous hand drawn images of systems and references to many books.
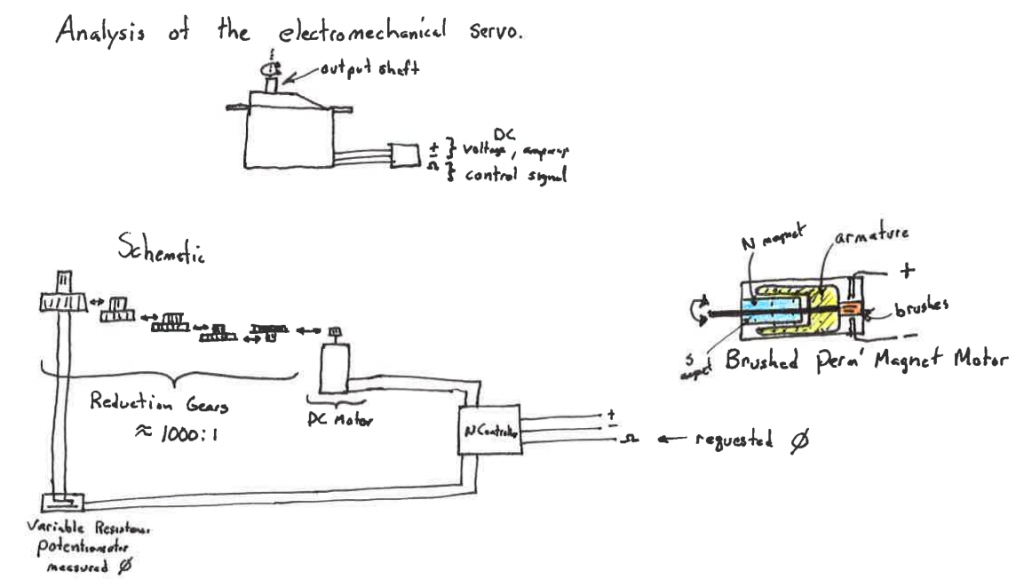
Detailed Aircraft Systems of Particular Aircraft were analyzed through flight manuals, NTSB accident reports, AIAA case-studies, and expert guest lectures.
- Cessna 170 & 310
- Gossamer Condor
- VTOL: VJ101 and VAK191B
- X15
- WW2 Dam Busters (system development case study)
- THAAD
- DHC-7 (aka. EO-5C / RC-7B)
- A behind-the-scenes guided tour of the Southern Museum of Flight in Birmingham by two (2) PhDs in History and Engineering.
The course also included a set of lectures titled “Failure Fridays” which investigated aircraft incidents and accidents by tracking the failure points and symptoms with a special emphasis on systems. These included:
- Cessna 182 Fuel Contamination
- Alaska 261
- A320 Fly By Wire
- Boeing 737 Rudder Actuator
- TWA 800
- Diesel Bug
- Advisory Circulars (AC)
- Patriot Missile
- Ariane 5
- The largest non-nuclear explosion known to man. (Not aerospace, but still an impressive and covertly intentional systems failure!)
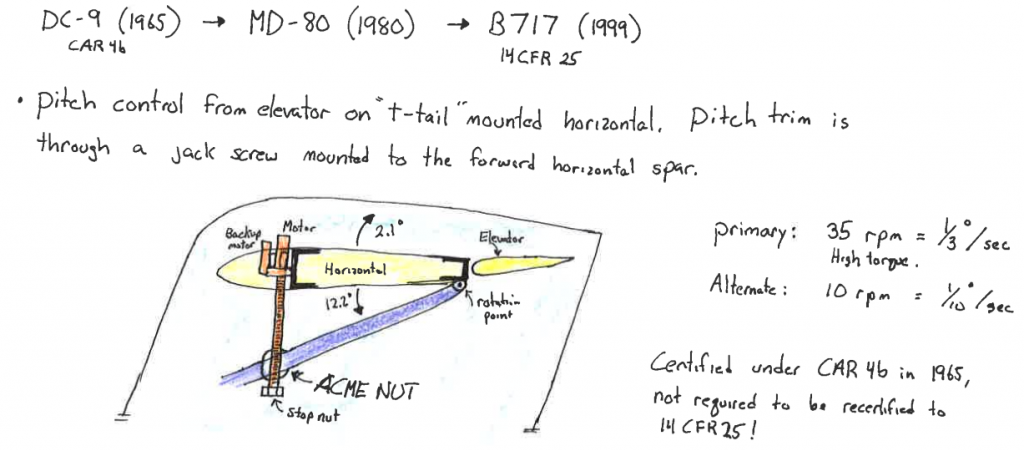
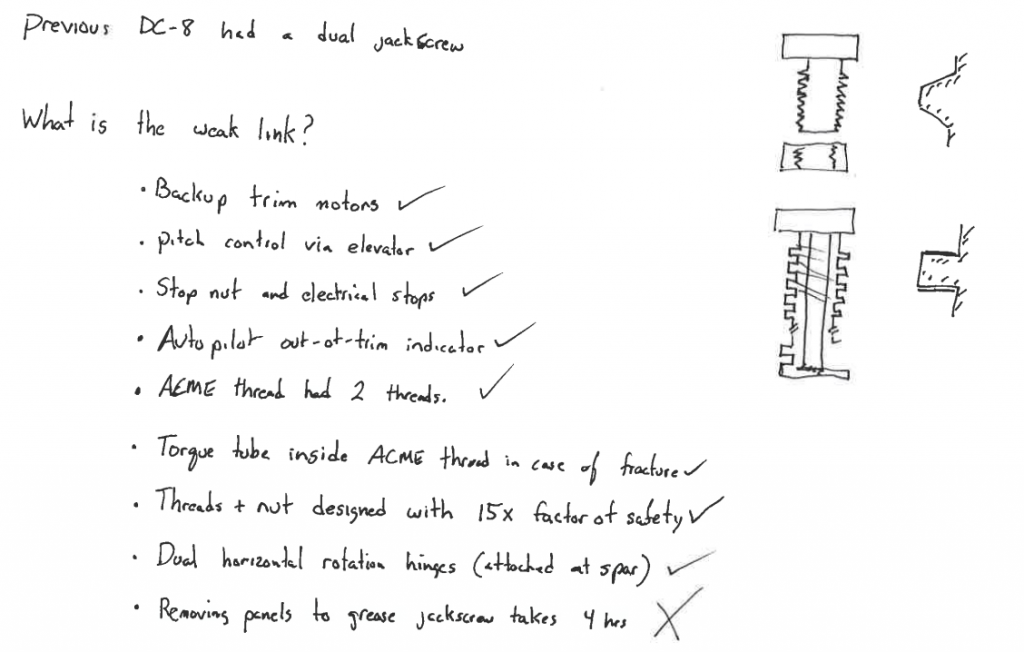
This course was particularly interesting; as the instructor, I learned a great deal about many topics. I had to work hard to stay ahead of the students. The students gave one of the best ratings that I have ever received. One student said:
The course was very interesting and likely one of the most valuable classes I have had in college. Rather than sticking strictly to theory as most of the Aerospace curriculum does, this class covers details about the what, why, and how for a wide range of
systems that will be particularly useful in any aerospace career.
Another student said:
This course provided me with an otherwise unobtainable insight into the real world of engineering systems, something not talked
about in other courses. This class is great for the industry engineer.
Not every comment was so positive. One student mentioned that this course required several prerequisites and that “newly transferred” students would find the course “difficult”.
More information and the full course notes are available by contacting Charles O’Neill.